WIldsense Ltda. develops an IoT sensing system to assist in the extraction of data and relevant information in critical processes related to agricultural cultivation, specifically in fruit production.
These processes include monitoring the performance and behavior of harvesters, determining fruit ripeness and quality, making production projections, and sensing the pressure at different irrigation sites. The goal is to implement a modular system in the industry that allows the various associated services to be packaged, in order to provide a service that can be tailored to the needs of different properties and clients in a pilot study.
Priority projects to be developed
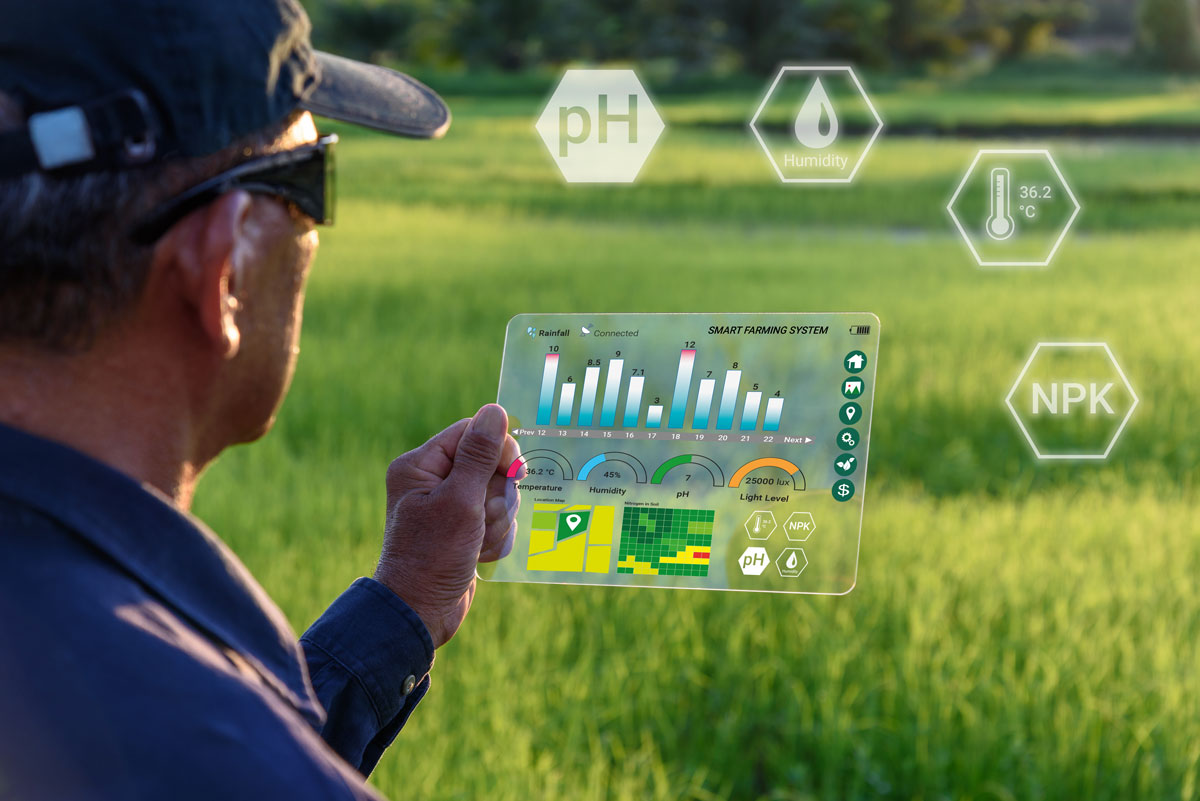
Harvester monitoring.
The goal is to track harvesters to capture information such as their daily route, how much fruit they harvested, and their health status throughout the workday, among other things. Therefore, Wildsense proposes the use of a low-cost smart band or bracelet, which will transmit all this information to a central system for processing and subsequent analysis.
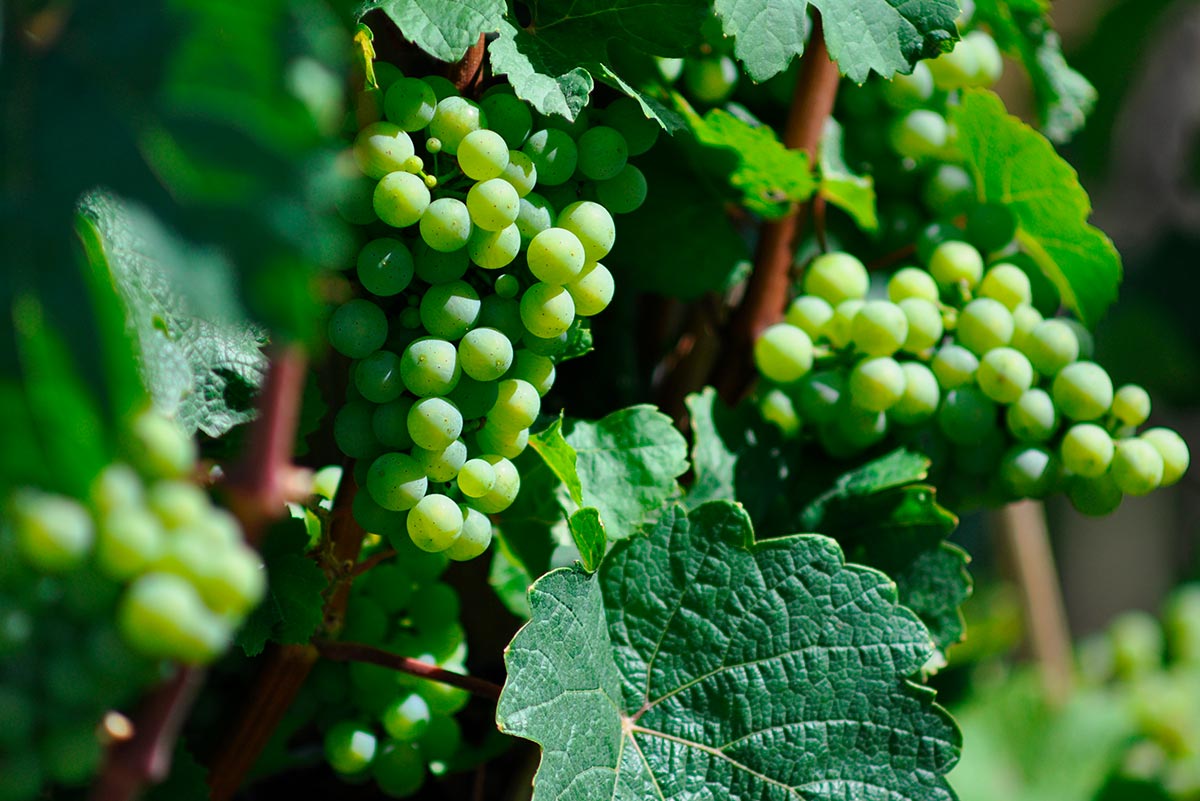
Image processing, videos of fruit ripening and quality.
The goal is to track harvesters to capture information such as their daily route, how much fruit they harvested, and their health status throughout the workday, among other things. Therefore, Wildsense proposes the use of a low-cost smart band or bracelet, which will transmit all this information to a central system for processing and subsequent analysis.
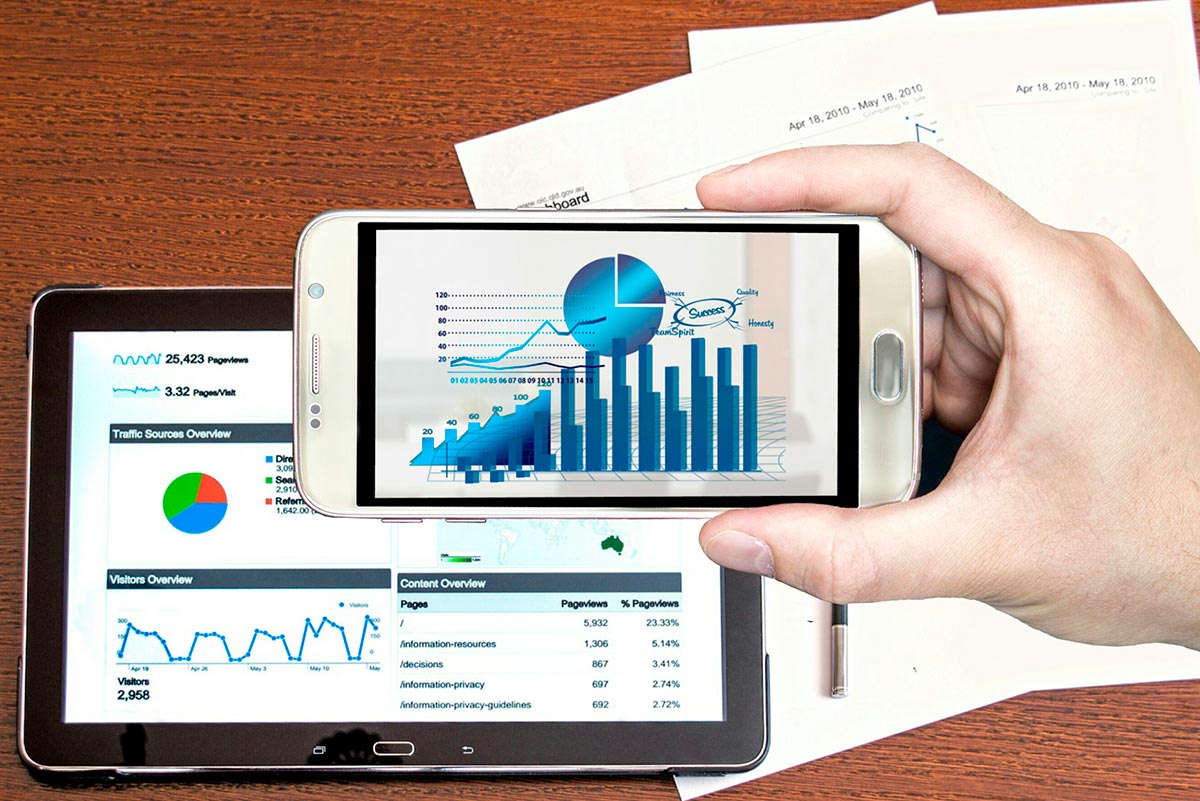
Data analysis and projections for decision-making.
The goal is to analyze all the information collected by the network of sensors, cameras, GPS, fruit ripening and quality, and the harvesters’ work, among other features, in order to make projections and estimates of production for future months. To do this, all system components will be connected to the main class, which will perform these analyses and estimates and send them through different channels to be later viewed in various applications. Some of these include being able to view the progress of the plantations or the work performed by a harvester, among others.
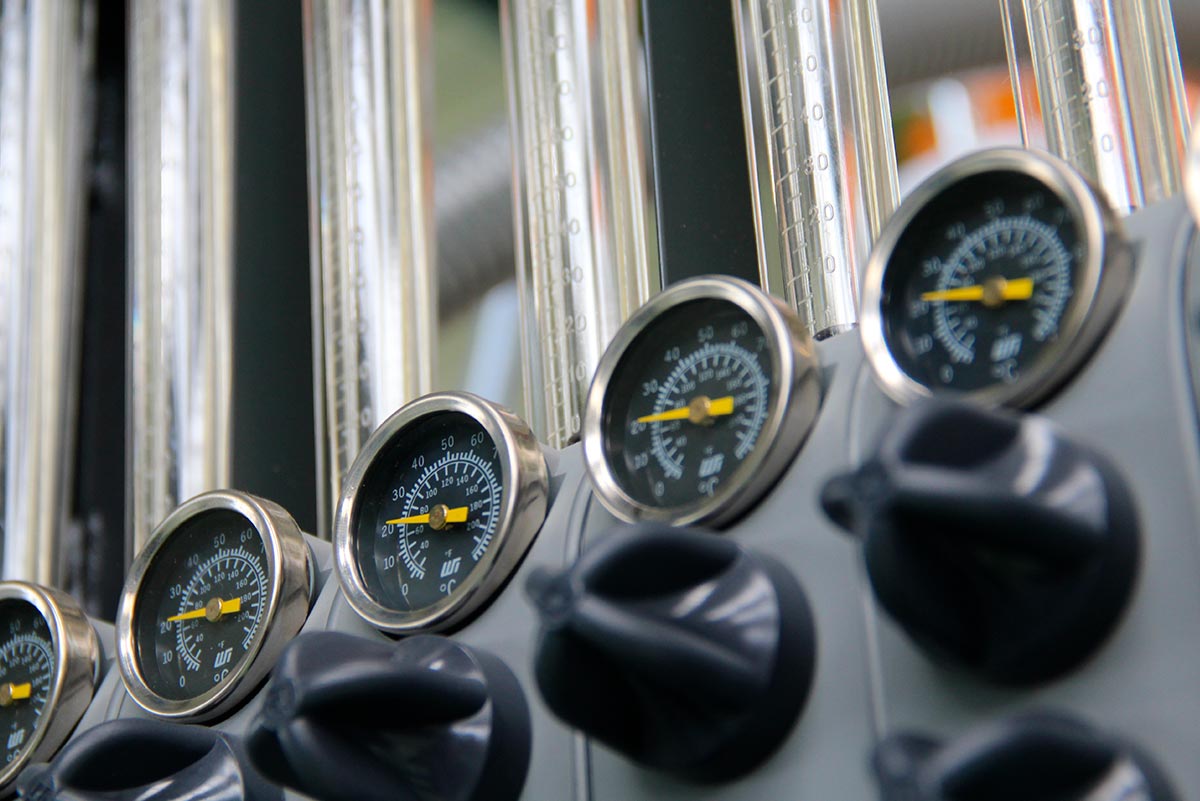
Sensorization to obtain irrigation canal pressure.
One problem encountered in crop irrigation is water pressure, which varies between the source and destination, resulting in a loss of control over the cultivation process and misuse of water resources. For this reason, a system for monitoring and sensing irrigation canal pressure is proposed.
Solution
A multimodal IoT sensing system is proposed to extract and integrate relevant information in critical processes associated with agricultural cultivation, with an emphasis on fruit production. The system must be able to solve the aforementioned problems. It is worth mentioning that due to the size of the crops and the technology used, it is impossible to connect the entire network of sensors, cameras, and GPS directly to the main module of the system. Therefore, it was decided to separate the fruit fields into different sections shaped like hexagonal cells, as can be seen in the following image.
This allows for a better distribution of the different sensors, since there are both stationary sensors, as mentioned above, and mobile ones. Each sector will have a “Base Station,” which will be responsible for connecting all the sensors within the cell and collecting the information provided by each sensor component. Finally, the main module, located in the Core Layer, will be responsible for connecting to each base station to collect information on all the crops present. The WildSense architecture and the problems detected are described in more detail below.

System Architecture.
Since the sensor network uses different access technologies, a system is proposed where the access layer has data reading interfaces specifically designed for each type of network or communication protocol used by each sensing component.
The following diagram shows at least three access technologies: MAVLINK for drones, and Wi-Fi and LoRaWAN for the rest of the sensors.
LoRa Network Architecture.
The size of the land is highly variable from hundreds of meters to kilometers in length. This fundamentally depends on the type of fruit that is harvested and the geographical location.
For example, the fruit fields in Chile are much smaller than those in Peru. Therefore, the choice of network technology becomes a challenge. As a result, it is proposed to use LoRaWAN for the network, because this new communication technology has been created for Low Power Wide Area Network (LPWAN) and it is relatively cheap to cover a new area with devices compatible with this technology.
The communication range has become the critical part in most IoT systems and with the appearance of this technology, more than km can be reached in rural areas with very low power consumption.
LoRa covers the physical layer for wireless communication, while LoRaWAN establishes the communication protocols and network architecture which determine the lifetime of nodes, network capacity, quality of service, security, and wide variety of applications supported by the network.
LoRa is capable of managing many nodes in multiple locations within the area, unlike Wi-Fi based systems for example, which need to have many access points to increase the coverage area.
The combination of LoRa and WiFi technology reduces the cost of IoT system deployment. In addition, LoRa uses the Industrial, Scientific and Medical (ISM) frequency bands that do not require a license to use, which accelerates the deployment and implementation of the network.
The figure below shows the general architecture of a LoRa network which is made up of four fundamental elements: LoRa nodes, gateways, network server and application servers.
..Arquitectura general de una red LoRa.
If an analogy is made with our scenario, the LoRa nodes would be the bands/wristbands capable of transmitting all the necessary information to the gateways using a chirp spread spectrum (CSS) modulation as defined in the LoRa physical layer.
This type of modulation is very efficient in terms of energy consumption, similar to the frequency shift keying (FSK) modulation used in most wireless communications, but it also allows reaching great distances.
The gateways must be properly deployed on the premises and are intended to receive messages from all nodes in their coverage area and forward them to the network server.
The connection between the gateways and the network server is made through a high-bandwidth network such as WiFi, Ethernet or cellular (3G/4G), unlike the connection between the nodes and the gateway that is carried out through the LoRaWAN communication protocol. On the other hand, the network server is in charge of routing the messages coming from the nodes to the specific application and vice versa.
Lastly, the application servers will have specific tasks depending on the requirements of the project. For example, one of them will be in charge of processing the signals coming from the bands/bracelets to determine the position of the harvesters at each instant of time.
The number of elements that make up the network and the best way to distribute them depends on the work scenario, the number of tasks that are going to be executed in the network and the precision that is to be achieved.
Each harvester would wear a band/bracelet representing the mobile nodes. For simplicity, ChirpStack (https://www.chirpstack.io/) was chosen as the network server and there will be an application server associated with each of the specific objectives of the project.
The gateways that must be deployed on the premises to guarantee the performance of the multimodal system depend on the desired precision in the location of the nodes and, therefore, will be closely related to the implemented algorithm.
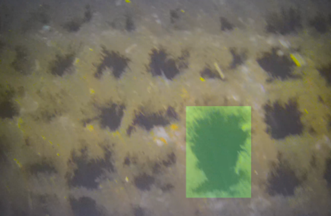
Location in LoRa networks.
The location techniques applied to LoRa networks follow the same principles used in traditional wireless networks. Firstly, a Global Positioning System (GPS) could be used to determine the position of each harvester on the farm, although this is not always feasible because trees can limit coverage and, more importantly, significant energy consumption is required. for a wearable device like a band/wristband.
As a consequence, it is proposed to use other techniques that dispense with GPS, which are divided into range-based or range-free. Rank-free solutions are used to estimate the behavior of groups of nodes and are therefore not suitable for accurately tracking each harvester.
On the other hand, range-based solutions are the most feasible, since they are based on determining the position of the target node with respect to other reference nodes, through different techniques such as: Time of Arrival (ToA), Time Difference of Arrival (TDoA), Received Signal Strength Indicator (RSSI) and Angle of Arrival (AoA).
Solutions based on the RSSI parameter are the simplest to apply, since it is only necessary to estimate the power of the received signal assuming the transmission power is known. Thus, the distance traveled by the signal depends on the propagation model that best fits the work scenario.
Having the distance from each harvester to one or more reference nodes (gateways) it is possible to form circles with center in the node to locate and the radii will represent the previously calculated distances. The position of the harvester is determined through the intersection of these circumferences, which is known as trilateration or multilateration.
This solution has the disadvantage that it is not easy to accurately determine the relationship between the attenuation of the signal power as a function of the distance traveled and, therefore, a location error would be incurred.
On the other hand, solutions based on AoA are more complex to implement because the angle of arrival of the signal must be obtained, which is possible using a multiple antenna system.
Using or more gateways, lines are drawn with the appropriate angle and the intersection represents the position of the harvester, which is known as triangulation. The disadvantage of this method lies in the complexity of the receiver design and the processing of the received signal.
The operating principle of the ToA technique consists of calculating the time it takes for the signal to propagate from the band/wristband to one or more gateways. With each time and knowing the speed of propagation of an electromagnetic wave in the air (m/s), the relative distance between each harvester and the corresponding gateway can be calculated. The last step is to apply trilateration to determine the position of each harvester.
The main disadvantage lies in guaranteeing a perfect synchronization between the transmitter and the receiver, to accurately calculate the time of flight of the signal. For example, a time measurement error of ns is equivalent to a distance of m.
The TDoA method is based on calculating the difference in the propagation time of the signal from the band/wristband to each gateway. With this time difference, the difference in distances can be calculated, which then allows the construction of a series of hyperbolas associated with each difference in distance between the band/bracelet and the corresponding gateway.
The point where or more hyperbolas intersect, corresponds to the position of the harvester. This solution only requires synchronization between the gateways to calculate the difference in arrival time, which is an advantage since LoRa technology defines its own strategies for synchronization. This makes TDoA the most favorable solution to implement for locating and monitoring harvesters on farms.
The figure below represents the proposed model, where the central circle represents a band/wristband with support for LoRa, the three communication towers are equivalent to the minimum number of gateways that, as shown, are complemented by GPS to guarantee synchronization, and the network server routes the messages coming from each gateway to the application server (for example: Geolocation Solver) where the algorithm for harvester location will be implemented.
Read More
Proposed model for the positioning of harvesters.
Infrastructure for image processing and data analysis.
There are other objectives that are somehow supported by the network infrastructure that is proposed to be created to determine the location of the harvesters. One of them is the use of complementary technologies for bands/bracelets that make it possible to extend their use to access control, identification and registration of the daily production of each individual. For this task, the Radio-Frequency Identification (RFID) or Near-Field Communication (NFC) connectivity technology is proposed.
Low power consumption is essential because we would have a large number of bands/bracelets and, therefore, the time between each battery recharge should be as long as possible. The way to extend the life of batteries is through energy conservation or energy harvesting techniques.
The first aims to maximize the time or the number of operations that can be carried out with the available energy, and the second complements the operation of the devices with energy sources from the environment, such as the sun or electromagnetic waves, among others.
The way to collect, store and process all the data coming from the sensors for decision making can be addressed with a mobile station.
This mobile station contains a digital scale to deposit the harvested fruits and associate each load with a user via RFID. This solution can include photo/video cameras to monitor the evolution of the fruits in the production process.
Through this method you can have a more accurate record of production, and perform better planning and decision making.
Software Architecture.
There is a 3-layer microservices system:
- Access, where sensing components are accessed through input and output interfaces (APIs).
- Central, where the processing services are.
- User, where are the user applications that require the previous layers.